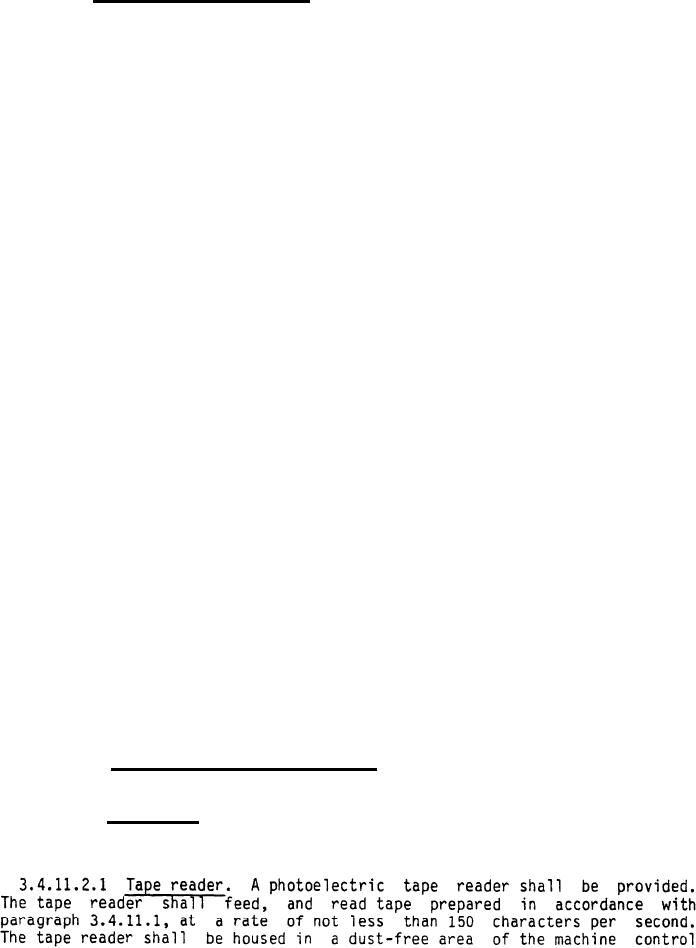
MIL-P-80054D
3.4.11 Numerical control system, The numerical control system shall be of
the solid state, soft-wired, micro processor, computerized numerical control
type. The system shall provide automatic control of machine functions,
operating modes, punch selection, and two axes control of the horizontal " X "
and "Y" motion, When a plasma - arc or carbon dioxide laser cutting head is
furnished, the cutting head shall also be controlled by the CNC unit, The
axes shall be identified in
accordance with EIA standard RS-267. The
control shall be a positioning and contouring type having linear and circular
interpolation, capable of simultaneous two axis contouring. Unless executive
program routines are provided in nonvolatile memory form (i. e. bubble memory
cassette, hard disc, etc), the control unit shall be provided with absolute
and incremental programming. Control features shall include buffer storage,
part program storage, program edit capability and control diagnostics. The
control unit shall direct machine functions from part program data in memory
storage, punched tape, and manual data input. The control shall initiate a
halt or an error signal should a fault condition occur in the control, All
necessary executive program routines shall be furnished in the form of 1 inch,
eight channel, binary coded decimal punched tape for controls having volatile
memory. A line voltage variation of + 10 percent from normal shall not
adversely affect the control system functins, The control shall function in
ambient temperatures ranging from 50 degrees F to 110 degrees F and relative
humidities ranging from 5
percent to 95 percent. The control
shall
automatically shut down when internal operating temperatures exceed safe
operating temperature. Control resolution shall be not greater than 0.001
inch for each linear axis. The auxiliary functions of the system shall
include, not less than the punch action and opening and closing of the
workpiece clamps. The system shall be provided with operational interlocks
and functional protection to prevent the machine from operating when the
turrets are not locked in the punching position, the machine drive brake is
not released, or the air pressure of the machine or auxiliary drive units
drops below the required operating level. Interlock circuitry shall also be
provided for assuring sequential operation of the system, The control unit
shall rotate the turrets, lock the programmed punch and die station in the
punching position, and position the workpiece throughout the full range of
travel along the "X" and "Y" axes of motion. The control unit shall
automatically control the acceleration and deceleration of all axes of motion.
The control unit shall control axis movements individually, simultaneously, or
in any combination. The control unit shall control the positioning units for
accomplishing any function within the capacity of the machine without loss of
cycle synchronization. The smallest program increment for positioning the
workpiece shall be not more than 0.001 inch and the largest shall be not less
than the workpiece positioning range specified in table I.
3.4.11.1 Peripheral equipment interface. Unless otherwise specified (see
6.2.1), the control shall be equipped with an interface complying with RS-232.
3.4.11.2 Data input. Unless otherwise specified (see 6.2.1), the data
input media shall be one inch, eight channel, punched tape in conformance with
EIA Standards RS-227, RS-244, RS-274 and RS-358.
11
For Parts Inquires call Parts Hangar, Inc (727) 493-0744
© Copyright 2015 Integrated Publishing, Inc.
A Service Disabled Veteran Owned Small Business