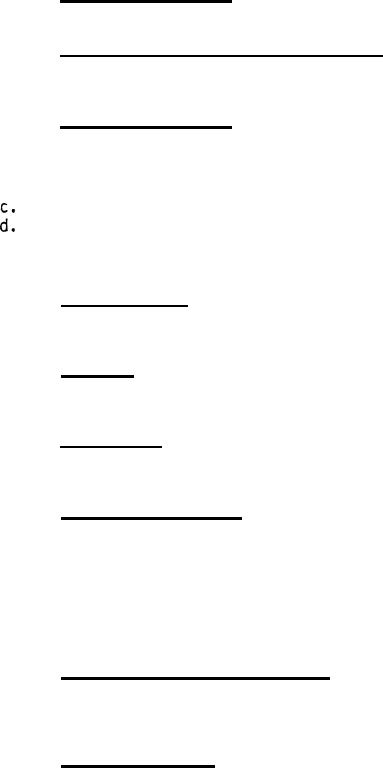
MIL-P-80054D
3.4.11.19 Block-by-block read. The control shall have a block-by-block
read function to provide for reading information one block at a time.
*
3.4.11.20 Lead and reversal error compensation. Lead error and reversal
error compensation shall be provided to permit data to be stored in the
control to compensate for errors and backlash of each linear axis.
The following additional control features
3.4.11.21 Additional features.
shall be provided:
a.
Four quadrant programming.
b.
Incremental and continuous jog for each axis.
Leading zero suppression or decimal point programming.
Inches per minute (IPM)/millimeters per minute (MMPM),
programing in all modes of operation.
Pattern repeat.
e.
3.4.11.22 Reference zero. The control unit shall have a reference zero to
move each axis to a reference limit switch to establish synchronization and
reset all registers to zero.
3.4.11.23 Set zero. The control unit shall have a "set zero" feature to
permit the specified axis register to be reset to zero establishing present
axis location as zero.
3.4.11.24 Tape tryout. The control shall have a tape tryout feature to
permit new part programs to be read through the control without machine mo-
ions.
3.4.11.25 Operational software. Operational software shall be furnished
with the control and shall contain all logic necessary to effectively operate
the machine tool. The software shall be provided either resident in the
control in the form of nonvolatile memory or separately in the form of one
inch, eight channel, binary coded decimal punched tape for controls having
volatile memory. In either case, the software shall be provided
for
meaningful diagnostic relating to the use of the controls, machine tool part
program and operator's actions.
3.4.11.26 Maintenance diagnostics system. Maintenance diagnostics software
shall be furnished to provide for diagnostic checking of the machine control
unit. The diagnostic software shall test, exercise, and display failures to
not less than board level.
3.4.11.27 Positioning units. The primary command functions of the system
with
shall be accomplished by turret and workpiece positioning units
positioning ranges and speeds to comply with table I. Positioning unit travel
shall be obtained by electric motor driven anti-backlash ballscrews and nuts.
Response of the positioning units to the primary commands for starting and
stopping and the rate of motion shall be such that the specified punching
accuracy is maintained. Except for sizes 1 and 3, which may be uni-
directional, the turret positioning unit shall be provided with hi-directional
turret rotation capability for automatically rotating the turrets in the
direction for which the distance is shortest between the programmed punch and
die station and the punching
position under the ram. The
workpiece
14
For Parts Inquires call Parts Hangar, Inc (727) 493-0744
© Copyright 2015 Integrated Publishing, Inc.
A Service Disabled Veteran Owned Small Business